
Inventory Warehouse Management
Last updated on 1/25/2023Implementing a solid process for managing warehouse inventory is imperative for any business that sells tangible goods. It helps you not over-buy or over-produce, while also ensuring you always have enough stock on hand to meet orders quickly. Warehouses are set up to optimize order fulfillment, but it’s your job to make sure there is stock to distribute.
Best Practices for Managing Warehouse Inventory
Below are processes to implement when managing warehouse inventory.
1. Track Inventory and Control Stock

To have the best handle on your warehouse inventory, you must keep a log that tracks your inventory’s stock. Controlling your stock mitigates over-purchasing or under-delivering on products, which can both lose you money.
The best way to track inventory and control stock is to use software or an app that specifically manages inventory. Not only do these tools track your inventory, but they usually have other special features, such as optimizing inventory levels, creating inventory reports, and even forecasting inventory demands.
Below are popular inventory management software tools to try:
- Cin7 - Overall favorited software
- Lightspeed Restaurant - Best for restaurants
- Ordoro - Best for multichannel e-commerce sellers
- inFlow - Best for B2B and/or wholesale companies
- Katana and Megaventory - Best for manufacturers
- monday.com - Best free software
2. Prioritize Warehouse Slotting
Warehouse slotting is a layout optimization practice. This simplifies gathering inventory as it’s based on storing the most frequently purchased items near each other for quick picking and packing.
Warehouse slotting can also be organized by stocking inventory based on characteristics such as size, weight, product type, and order history. However, the most common way to organize slotting is by placing the most frequently purchased items near the packing tables so your business can achieve quick order fulfillment.
3. Invest in a Warehouse Management System
If you want to determine how your operations are performing in your warehouse, then invest in a warehouse management system (WMS). Having this operations performance report gives you great insight into what’s happening day to day within your order fulfillment processes: if your packing stations are incorrectly packing, if orders are shipped on time, and even the rate at which your employees fulfill orders hourly. Additionally, recording hourly order fulfillment allows you to staff accordingly for future months based on how many orders you plan to fulfill.
4. Choose a Picking and Packing Process
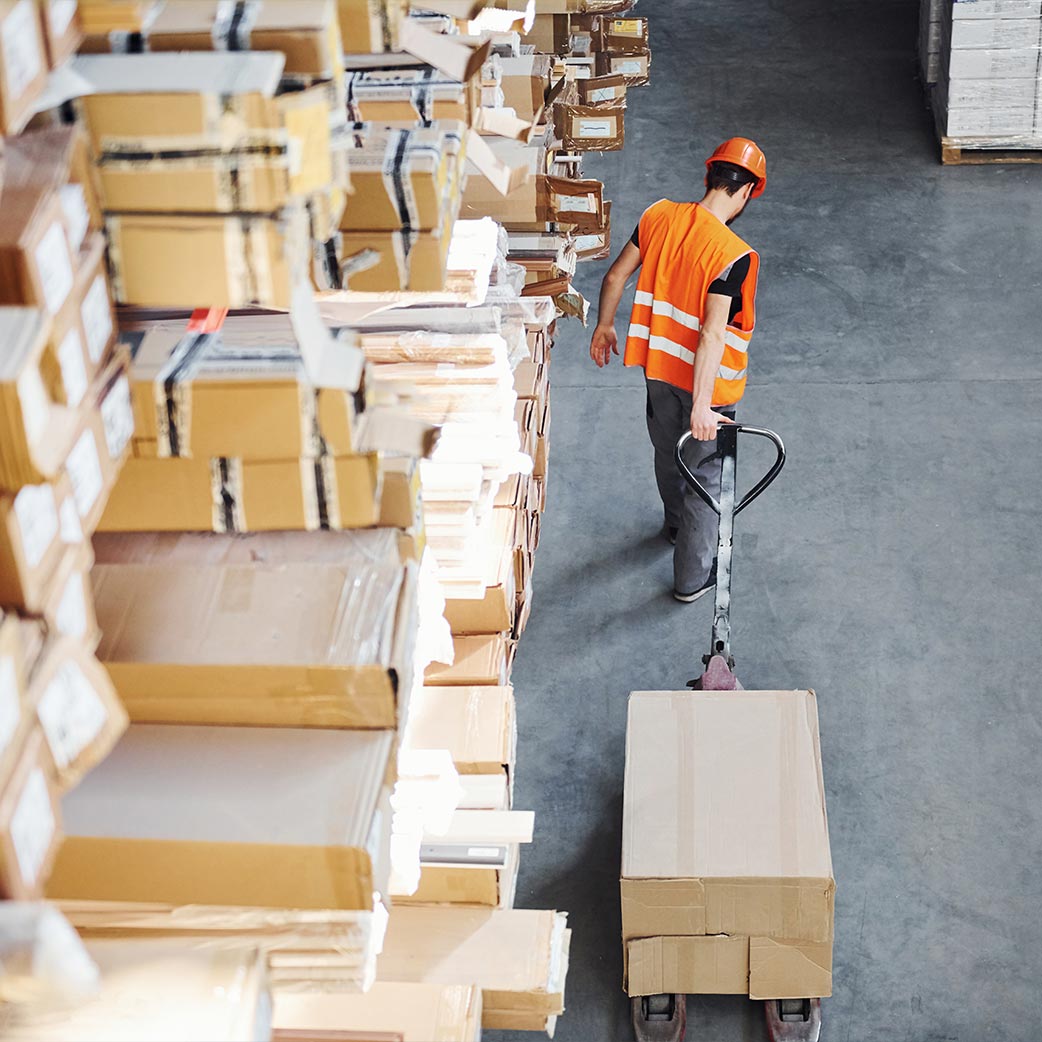
Pick and pack is a warehouse term for picking the items that are in a customer’s order and then packing those items efficiently for shipping. This step is crucial in order fulfillment as it not only involves getting your customer’s order right but ensuring it is sent out quickly to gain or sustain customer satisfaction.
There are a few different picking and packing processes you can implement in your warehouse:
- Discrete Picking - This is the most common process as it’s the most simple to understand. Discrete picking is when one person picks every item in an order and completes one order at a time. While easy to implement and understand, this can also be one of the most time-consuming processes.
- Zone Picking - Zone picking is when a picker is designated to one area of the picking stations and picks the items in that station to complete an order. This way, pickers can become fluent in their picking station, taking less time to find items and reducing miss-picks.
- Wave Picking - Wave picking is like discrete picking but is a schedule-based process. Orders are scheduled for picking at certain times of the day, taking into account ship dates, delivery times, and carrier pick-ups. This benefits employee labor and shipping times.
- Batch Picking - Batch picking, also known as cluster picking, is when a picker retrieves multiple SKUs at once instead of several pickers retrieving that item multiple different times. As long as you have the data right, this cuts down trips for your employees.
5. Conduct Control Checks
Conducting control checks of your inventory now and again is vital to quality. Items can break, expire, or be recalled. Inventory control checks are vital if you are shipping food, even more so with perishable foods. Doing this helps you have a better understanding of your current inventory and also will keep your customers satisfied when ensuring no expired or broken items are being sent to them.
6. Encourage Employees

Lastly, make sure to check in with your warehouse employees. A good manager asks for feedback to improve their employees' quality of life while at work to be more comfortable getting the job done. Also, ask them if they have noticed any ways to improve efficiency and order fulfillment accuracy. Who knows this better than the people who do it every day?
If you want your business to succeed, implementing inventory warehouse management best practices is crucial to not over-buying, under-distributing, and ensuring that orders are met efficiently and accurately. Whether it's a big box store or a small business shipping its goods, there are many different best practices to implement for order fulfillment.